In the ever-evolving landscape of industrial automation and motor-driven systems, the demand for accuracy, durability, and adaptability has never been higher. Companies across sectors—automotive, aerospace, renewable energy, and robotics—rely on advanced testing and control mechanisms to ensure their products meet stringent performance standards. Among the unsung heroes of this technological revolution are hysteresis brakes, hysteresis dynamometers, hysteresis clutches, and motor testing systems. These components form the backbone of modern motor test equipment, enabling engineers to push boundaries while maintaining precision.
THE SCIENCE BEHIND HYSTERESIS TECHNOLOGY
At the heart of hysteresis-based devices lies a simple yet profound principle: the magnetic hysteresis effect. When a magnetic material is subjected to a varying magnetic field, it resists changes in magnetization, creating a controllable torque or braking force. This phenomenon eliminates mechanical contact, reducing wear and tear while delivering smooth, consistent performance.
Hysteresis brakes, for instance, are prized for their ability to provide precise torque control without the friction losses typical of traditional mechanical brakes. They excel in applications requiring delicate tension control, such as wire winding, textile manufacturing, or medical device assembly. The absence of physical contact between components ensures minimal maintenance and a lifespan measured in decades, not years.
Similarly, hysteresis dynamometers leverage this principle to measure and absorb power from rotating systems. Unlike eddy current or water brake dynamometers, hysteresis models offer linear torque-speed characteristics, making them ideal for testing electric motors, turbines, or hybrid vehicle drivetrains under variable load conditions.
BREAKING DOWN MOTOR TEST SYSTEMS
A comprehensive motor test system is more than a collection of instruments—it’s an ecosystem designed to simulate real-world operating conditions while capturing critical performance data. Modern systems integrate hysteresis components with advanced sensors, software analytics, and automation protocols to deliver end-to-end testing solutions.
Key elements include:
- Motor dynamometers for load simulation
- Torque and speed sensors with microsecond-level response times
- Thermal monitoring systems to track efficiency losses
- Customizable software interfaces for data visualization
Consider an electric vehicle manufacturer validating a new powertrain. Using a hysteresis dynamometer paired with regenerative energy recovery systems, engineers can replicate hill climbs, sudden accelerations, and regenerative braking cycles—all while measuring efficiency, heat dissipation, and component fatigue. This data directly informs design improvements, warranty assessments, and compliance reporting.
HYSTERESIS CLUTCHES: THE UNSUNG HEROES OF MOTION CONTROL
While brakes and dynamometers often steal the spotlight, hysteresis clutches play a pivotal role in applications requiring slip control and overload protection. These clutches transmit torque through magnetic fields rather than physical engagement, allowing for:
- Shockless torque transmission in printing presses
- Precise tension control in film extrusion lines
- Overload prevention in robotic assembly arms
A food packaging line, for example, might use hysteresis clutches to maintain consistent wrapper tension despite sudden speed changes. If a jam occurs, the clutch slips protectively, preventing motor burnout and production downtime.
ADVANCEMENTS IN MOTOR TEST EQUIPMENT
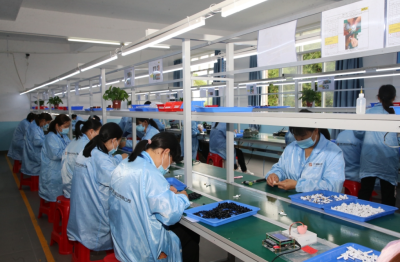
The latest generation of motor test systems incorporates AI-driven predictive analytics and IoT connectivity. Imagine a cloud-enabled hysteresis dynamometer that not only tests a motor but also predicts its maintenance needs based on harmonic distortion patterns or bearing vibration signatures. Such systems are transforming quality assurance from a reactive process to a proactive strategy.
Modular designs now allow seamless integration with existing production lines. A mid-sized drone motor manufacturer, for instance, could deploy a compact hysteresis-based test bench that automatically adjusts test parameters for different motor sizes—from micro UAV rotors to heavy-lift propulsion systems—without hardware swaps.
CASE STUDY: WIND TURBINE GENERATOR TESTING
To illustrate these technologies in action, consider the challenge of testing a 5MW offshore wind turbine generator. Traditional methods involving hydraulic load banks are cumbersome and energy-inefficient. A hysteresis dynamometer solution offers:
- Bi-directional testing for both motor and generator modes
- Energy recovery capabilities feeding power back to the grid
- Salt spray-resistant construction for maritime environments
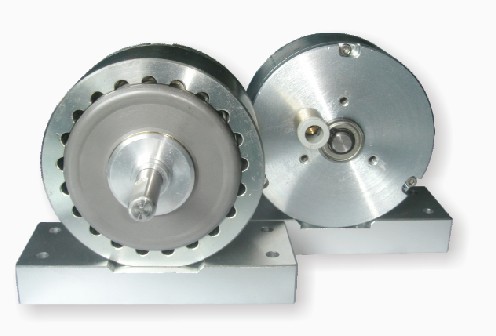
During a recent project, engineers used a hysteresis-based system to simulate 20-year wear cycles in just eight weeks, identifying insulation weaknesses in the stator windings before deployment. The result? Karl Mayer tensioner in warranty claims and optimized maintenance schedules.
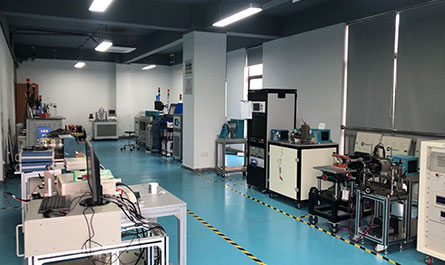
THE FUTURE OF HYSTERESIS AND MOTOR TESTING
As industries transition toward electrification and sustainable energy, the role of precision testing will only grow. Emerging trends include:
- Ultra-high-speed testing for aerospace applications (50,000+ RPM)

- Integration with digital twin platforms for virtual-physical testing hybrids
- Miniaturized hysteresis devices for micro-motor applications in medical implants
Manufacturers who invest in advanced motor test systems today position themselves to lead in markets where performance margins are measured in fractions of a percent. Whether it’s extending the range of an electric vehicle by optimizing motor efficiency or ensuring the reliability of life-saving surgical robots, these technologies form the invisible foundation of innovation.
In conclusion, the synergy between hysteresis-based components and intelligent motor test systems represents more than technical superiority—it embodies a commitment to quality that resonates through every product they help create. For engineers, procurement specialists, and R\u0026D teams, understanding these tools isn’t just about specifications; it’s about shaping the future of motion itself.